Прочность стала выше
Специалистам прокопьевского завода «Подземтрансмаш» (входит в состав холдинговой компании «СДС-Маш») удалось добиться значительного повышения прочности оборудования, которое подвергается капитальному ремонту, а также производится на предприятии. В частности, речь идет о деталях насосов и углесосов.
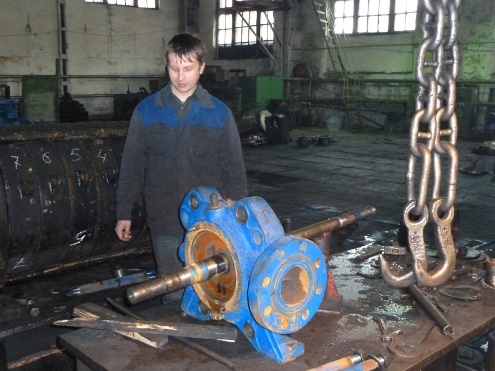
Сделать это дорогостоящее оборудование более износостойким прокопьевским машиностроителям удалось благодаря внедрению в технологической цепочке современных технологий.
Качество и экологичность
Обеспечивать более высокую прочность деталей, которые постоянно подвергаются повышенным нагрузкам, на «Подземтрансмаше» стали двумя способами. Первый предполагает использование порошковой проволоки. Второй - упрочняющих порошков. «Современные технологии выгодно отличаются от использовавшегося ранее метода наплавки электродами сразу по нескольким параметрам», - рассказывает начальник конструкторско-технологического отдела завода «Подземтрансмаш» Владимир Лукашев. Например, если прежний способ - наплавка электродами - производился при помощи ручной сварки, то наплавка порошковой проволокой осуществляется посредством полуавтоматической сварки. Это позволяет производить работы быстрее и качественнее. Кроме того, метод наплавки порошковой проволокой помогает существенно улучшить условия труда. «При сварке с использованием электродов в атмосферу неизбежно выделяются вредные вещества, - объясняет заместитель начальника конструкторско-технологического отдела завода «Подземтрансмаш» Владимир Карцев. – Они воздействуют на состав воздуха в цехе в целом и дыхательные органы сварщиков в частности. Теперь содержание вредных веществ в воздухе в производственных помещениях удалось значительно сократить. А все потому, что при использовании порошковой проволоки количество вредных веществ гораздо ниже, поэтому и влияние этого метода на окружающую среду значительно меньше».
Упрочняющий букет
Второй способ увеличения износостойкости деталей упрочняющими порошками, который обеспечивает поверхностям деталей принципиально новые прочностные характеристики - совершенно новая для «Подземтрансмаша» технология. Внешне это выглядит следующим образом: на газовую горелку закрепляется специальный бункер, в который помещают порошок. В его состав входят такие химические вещества (в том числе металлы), как углерод, хром, железо, молибден, медь, висмут, кремний и никель. Во время технологического процесса вместе с пламенем горелки упрочняющий порошок попадает на поверхность детали, создавая на ней «защитный» слой, который и позволяет увеличить износостойкость детали и, значит, сократить число ремонтов.
Если учесть, что каждый ремонт, это, во-первых, вывод оборудования из производственной цепочки, а во-вторых, дополнительные затраты, то упрочнение для угледобывающих предприятий – клиентов «Подземнтрансмаша» - чрезвычайно выгодно. Как утверждают специалисты, после процедуры упрочнения срок службы деталей между ремонтами увеличивается до двух раз. При этом использование упрочняющей обработки приводит к удорожанию ремонта всего на 10%.
«Обе технологии мы будем использовать для обработки деталей, подвергаемых абразивному износу, - продолжает Владимир Фёдорович. – Так, углесосы, которые функционируют в шахтах, работающих по методу гидродобычи, постоянно подвергаются ударам кусков угля. Износу в процессе трения подвержены и различные детали насосов.
Конечно, такие поверхности нуждаются в соответствующем упрочнении».
Уже в мае машиностроители изготовили из деталей, упрочненных методом наплавки, один углесос. Он был отправлен на испытания, где специалисты проверили соответствие деталей всем производственным требованиям.
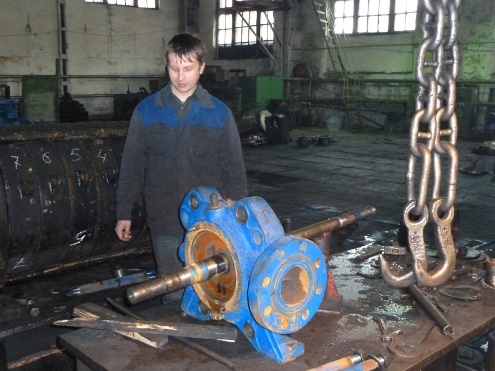
Сделать это дорогостоящее оборудование более износостойким прокопьевским машиностроителям удалось благодаря внедрению в технологической цепочке современных технологий.
Качество и экологичность
Обеспечивать более высокую прочность деталей, которые постоянно подвергаются повышенным нагрузкам, на «Подземтрансмаше» стали двумя способами. Первый предполагает использование порошковой проволоки. Второй - упрочняющих порошков. «Современные технологии выгодно отличаются от использовавшегося ранее метода наплавки электродами сразу по нескольким параметрам», - рассказывает начальник конструкторско-технологического отдела завода «Подземтрансмаш» Владимир Лукашев. Например, если прежний способ - наплавка электродами - производился при помощи ручной сварки, то наплавка порошковой проволокой осуществляется посредством полуавтоматической сварки. Это позволяет производить работы быстрее и качественнее. Кроме того, метод наплавки порошковой проволокой помогает существенно улучшить условия труда. «При сварке с использованием электродов в атмосферу неизбежно выделяются вредные вещества, - объясняет заместитель начальника конструкторско-технологического отдела завода «Подземтрансмаш» Владимир Карцев. – Они воздействуют на состав воздуха в цехе в целом и дыхательные органы сварщиков в частности. Теперь содержание вредных веществ в воздухе в производственных помещениях удалось значительно сократить. А все потому, что при использовании порошковой проволоки количество вредных веществ гораздо ниже, поэтому и влияние этого метода на окружающую среду значительно меньше».
Упрочняющий букет
Второй способ увеличения износостойкости деталей упрочняющими порошками, который обеспечивает поверхностям деталей принципиально новые прочностные характеристики - совершенно новая для «Подземтрансмаша» технология. Внешне это выглядит следующим образом: на газовую горелку закрепляется специальный бункер, в который помещают порошок. В его состав входят такие химические вещества (в том числе металлы), как углерод, хром, железо, молибден, медь, висмут, кремний и никель. Во время технологического процесса вместе с пламенем горелки упрочняющий порошок попадает на поверхность детали, создавая на ней «защитный» слой, который и позволяет увеличить износостойкость детали и, значит, сократить число ремонтов.
Если учесть, что каждый ремонт, это, во-первых, вывод оборудования из производственной цепочки, а во-вторых, дополнительные затраты, то упрочнение для угледобывающих предприятий – клиентов «Подземнтрансмаша» - чрезвычайно выгодно. Как утверждают специалисты, после процедуры упрочнения срок службы деталей между ремонтами увеличивается до двух раз. При этом использование упрочняющей обработки приводит к удорожанию ремонта всего на 10%.
«Обе технологии мы будем использовать для обработки деталей, подвергаемых абразивному износу, - продолжает Владимир Фёдорович. – Так, углесосы, которые функционируют в шахтах, работающих по методу гидродобычи, постоянно подвергаются ударам кусков угля. Износу в процессе трения подвержены и различные детали насосов.
Конечно, такие поверхности нуждаются в соответствующем упрочнении».
Уже в мае машиностроители изготовили из деталей, упрочненных методом наплавки, один углесос. Он был отправлен на испытания, где специалисты проверили соответствие деталей всем производственным требованиям.
Читайте так же